"НИиОКР по
патентам АТТ"
В "Демиурге" № 2 2004 г.
было опубликовано информационное письмо "О реализации интеллектуальной
собственности АТТ", в котором шла речь о проведении НИОКР по разработке
роторных агрегатов высокой удельной мощности (далее РАВУМ), являющихся
как отдельными узлами (компрессор, пневмопривод) роторного двигателя непрерывного
горения, так и собственно двигателем и сочетанным блоком двигателя с компрессором.
Финансирование осуществлял Фонд содействия развитию малых форм предприятий
в научно-технической сфере, в качестве производственной база (предприятие
- соисполнитель) выступил Свободинский электромеханический завод.
В ходе работ
был разработан и изготовлен действующий макет пилотного образца роторного
двигателя (ПОРД). Макет ПОРД (рис. 1) изготовлен из стали 10 и состоит
из двух легко разделяемых узлов: сжатия и расширения.
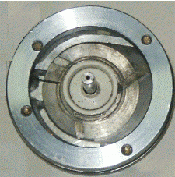
Рисунок 1. Узел
сжатия в сборке с прозрачной щекой (слева)
и детали узла расширения
макета ПОРД.
Узел сжатия был исследован
с использованием имевшейся в распоряжении измерительной аппаратуры общего
назначения. Макет узла сжатия (с производительностью 5 г/с при 3000 об/мин)
был рассчитан на выходное давление 0,5 МПа.
В результате
испытаний получена производительность узла сжатия 3,6 г/с вместо расчетных
5 г/с. Кроме того, вращающий момент в среднем оказался заметно выше ожидаемого.
С целью выяснения причин
указанных отклонений от расчетных величин одна из щек макета была заменена
щекой из органического стекла толщиной 10 мм. Модифицированный макет был
исследован в той же схеме и дал такие же результаты. В обоих случаях не
было зафиксировано заметное повышение температуры сжимаемого воздуха, как
прямыми измерениями, так и по отсутствию снижения давления за счет остывания
воздуха в ресивере после остановки двигателя.
Благодаря возможности
визуального наблюдения процессов было обнаружено, что перетекания воздуха
вдоль радиальных поверхностей ротора не происходит, ибо такое перетекание
было бы хорошо видно в масляной пленке в зазоре между радиальной поверхностью
ротора и щекой. В этом случае единственной причиной снижения производительности
могла быть утечка в зоне контакта между тангенциальной поверхностью ротора
и статором, где зона контакта была практически линейной. В обычных лопастных
насосах, в которых отсутствует сжатие, такая зона работает вполне удовлетворительно,
что, однако, оказалось несправедливым в нашем случае, так как в пределах
зоны существовал градиент давления.
Исследуя динамику вращающего
момента от угла поворота ротора, удалось установить, что резко повышение
трения лопастей в пазах ротора связано с несоответствием угла наклона лопастей
относительно радиусов ротора (рассчитаны на трение поверхностей с нитрид
- титановым покрытием), которое привело к возникновению в лопастях изгибных
усилий.
Таким образом,
в результате проведенных исследований макета:
1. Практически проверен
расчёт по коэффициенту трения между лопастями и статором угла наклона лопастей,
обеспечивающего минимальное значение изгибающего момента лопастей и, следовательно,
снижения трения лопаток в пазах ротора.
2. Выяснена необходимость
внесения изменений в конструкцию статора, обеспечивающих увеличение зоны
контакта тела ротора со статором. Подготовлены эскизы измененного статора
для конструктивно - технологической проработки соисполнителем.
3. Определены оптимальные
требования к измерительной аппаратуре и произведена закупка приборов и
части оборудования испытательных стендов на основе разработанных схем.
На основе этих испытаний
был изготовлен испытательно - демонстрационный стенд для исследования узла
сжатия в режиме компрессора, размещённый в легком алюминиевом чемодане
габаритами 400х300х150 мм.
Фотографии испытательно
- демонстрационного стенда узла сжатия
в транспортном (вверху)
и развернутом
виде.
На фотографии
показан внешний вид стенда, а на рисунке 2 - размещение элементов стенда
внутри чемодана. Для питания стенда достаточно бытовой электросети, что
позволяет проводить демонстрацию работы узла даже в кабинетных условиях.
Рис. 2. Схема
испытательно - демонстрационного стенда.
На рисунке 2 вверху
показано размещение деталей на крышке:
пневмосхема, включающая
возвратный клапан (1), манометр (2), предохранитель (3) и выпускной кран
(4).
На рисунке 2 внизу -
размещение деталей в основании чемодана, где находятся:
электродвигатель (1),
блок питания и управления двигателем (2),
тахоэлектрогенератор
(3) с вольтметром, градуированном в оборотах в минуту,
ресивер (4) с запорным
краном и испытуемый узел (5).
В демонстрационном режиме
электрические параметры работы двигателя (за исключением угловой скорости)
не контролируются. Стенд изготовлен и испытан на первом варианте макета
узла сжатия. Аналогичный стенд (с соответствующими схемными изменениями)
изготовлен для испытания узла расширения.
В процессе испытаний
макета на стенде проведены испытания узла сжатия, которые позволили обнаружить,
что реальная производительность макета составляет не более 70% расчетной.
После испытаний модифицированного узла (с прозрачной щекой) была выявлена
принципиальная конструктивная недоработка (малая тангенциальная протяженность
зоны контакта ротора и статора), устраненная затем при конструировании
опытного образца.
В результате дальнейших
исследований выявлена оптимальная степень изотермического сжатия применительно
к термодинамике процессов в двигателе. По полученным данным оптимален режим
с коэффициентом изотропного сжатия (геометрическое сжатие) kи
= 10. Это дает для изделия с показателем политропы, равным 1,2 (коэффициент
политропного сжатия kп
= 16).
Таким образом,
в результате проведенных НИиОКР, помимо чисто конструктивных и технологических
результатов были очерчены возможные области применения:
Для компрессоров
(узлов сжатия РДНГ) с электроприводом:
заполнение сжатым воздухом
баллонов объемом 40 л для запуска мощных дизелей (давление 15 МПа, мощность
привода 5,5 кВт, время заполнения баллона 15 мин)
заполнение сжатым воздухом
баллонов для аквалангов (давление 25 МПа, мощность привода 5,5 кВт, производительность
10 г/с)
аэрационных нагнетателей
в системах очистки (давление 60 - 70 кПа, производительность - 360 - 400
м3/час, перекачиваемая
среда - атмосферный воздух).
Для пневмоприводов
(узлов расширения РДНГ):
в качестве привода строительно-монтажных
инструментов (давление 0,8 МПа, расход воздуха 13 г/с, мощность 2,3 кВт).
Практические рекомендации
по применению других агрегатов семейства могут быть получены только после
завершения всего цикла испытаний пилотного образца РДНГ в целом.
К сожалению,
в связи с организационно-финансовыми трудностями предприятия-соисполнителя
(Свободинский электромеханический завод, г. Курск) в договорные сроки не
был завершен последний этап порученных соисполнителю работ, а именно, не
закончено изготовление пилотного образца.
В настоящее время работы
приостановлены в связи с отсутствием финансирования.